We believe that Rubber Right Rollers offers you the finest rubber rollers in the industry. With our modern manufacturing equipment and experienced staff, our customers know they can depend on us for a superior product. Our standards for quality, cost effectiveness, and outstanding customer service have remained constant since our foundation.
We are capable of manufacturing rubber rollers from .125” wide to 160” wide in a vast array of colors and durometers. We stock rubber roller materials in Neoprene, Nitrile, EPDM, Hypalon, Natural and Polyurethane to meet expedited delivery requests.
Some of the industries we serve are:
Paper, Film, and Foil Converters, Flexographic, Gravure and Offset Printing, Corrugated Box Textile, Metal, Packaging, Extrusion, Lamination, and Plastics.
Our Compound Comparison Chart will help you to select the perfect material for your rubber roller application.
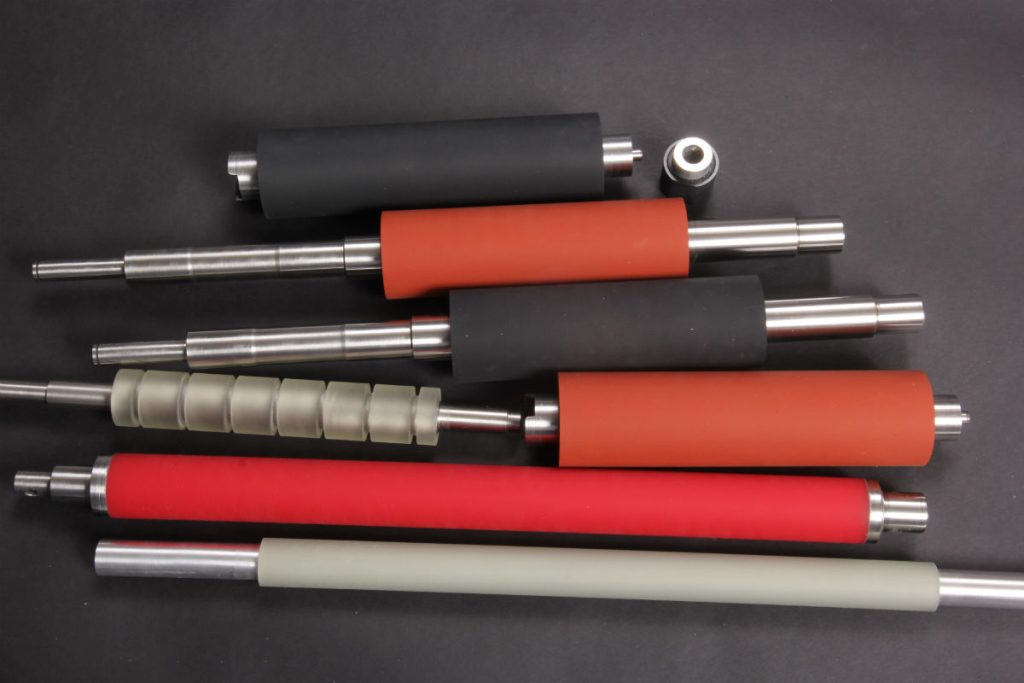
Commonly Used Rubber Roller Compounds
Carboxylated Nitrile - Excellent abrasion resistance, toughness, and tear strength. Excellent chemical resistance to aliphatic hydrocarbons (Oils). Maximum service temperature is 275 F. Major uses are for tough mechanical applications.
EPDM - Excellent chemical resistance to ketones, esters, acids, and caustics. Maximum service temperature is 350 F. Major uses are for chemical, heat, ozone, and UV light resistance. Used in coating, laminating, and flexo printing applications.
EPDM/Silicone Blend - This blend increases the release in EPDM and the toughness in Silicone. This gives you a good balance of heat and release properties. Maximum service temperature is 375 F. Used in coating and laminating rubber roller applications.
Hydrogenated Nitrile - Outstanding abrasion resistance, toughness, and tear strength. Excellent chemical resistance to aliphatic hydrocarbons (Oils). Maximum service temperature is 350 F. Major uses are for tough mechanical and dynamic applications. Used in paper making, converting, embossing, laminating and in steel mills.
Hypalon - Superior abrasion, tear, pressure, and heat resistance. Maximum service temperature is 300 F. Major uses are for chemical, heat, and ozone resistance. Used in coating, laminating, converting, embossing, and extrusion rubber roller applications.
Natural - Excellent abrasion, tear, pressure, and denting resistance. Maximum service temperature of 212 F. Used in the paper making and converting applications.
Neoprene - Known for a good balance of all around physical properties and chemical resistance. Maximum service temperature is 250 F. Used in a wide variety of industrial rubber roller applications.
Nitrile - Good balance of all around physical properties. Excellent chemical resistance to aliphatic hydrocarbons (Oils). Maximum service temperature of 250 F. Used extensively in offset, web, and flexo printing. Other applications Include coating, laminating, paper making, and textile manufacturing.
Polyurethane - Outstanding abrasion, cut, and tear resistance. Also has high rebound, load bearing and resilience properties. Maximum service temperature is 212 F. Used in paper making, converting, embossing, coating, laminating and in steel mills and other tough mechanical applications.
Silicone - Used when heat resistance or high release is required. Maximum service temperature is 500 F. Used in coating, laminating, and extrusion rubber roller applications.